KYF
Employee-Friendly-Workplace
Occupational Safety
KYF deeply understands that “people” are the foundation of a corporation’s sustainable development.
KYF deeply understands that “people” are the foundation of a corporation’s sustainable development.
Occupational Safety
The company is responsible for building up a safe and healthy work environment for stakeholders. To implement occupational safety and health more systematically, all of the company’s business footprints have all introduced an occupational health and safety management system (ISO 45001:2018) to ensure steps – including product development, manufacturing, testing, and sales – during the operation process comply with occupational health and safety regulations and other related requirements for prevention of incidents.
Additionally, the company conducts risk assessments, internal audits, and external audits every year. Through Plan-Do-Check-Act (PDCA), the company continues to improve processes and enhance workplace health and safety protection measures to avoid occupation disasters caused by unsafe behavior, environment, and equipment as well as fulfill its responsibility to protect employee’s health and safety.
Material Topic | Occupational Health and Safety |
---|---|
Significance for the Company | The company needs to ensure that employees and contractors comply with health and safety regulations and standard requirements, build up a work environment of zero occupational injury or disaster, and protect workers’ health and safety to fulfill its responsibility as an employer and owner. |
Impact | 1. Corporate Image: A company that values employee safety and health is often seen as a trustworthy and reliable brand. This helps improve the company’s image and reputation, attracting more talent, customers, and investors. 2. Economic Impact: Employees in a safe and healthy work environment are more able to focus on their work. Reducing accidents and illnesses can lower the frequency of work interruptions, ensuring the continuity of production lines or services, and improving productivity and work efficiency. |
Policy and Commitment | KYF upholds the philosophy of “safety first, Zero occupational injury or disaster,” as well as taking care of employees’ physical and mental health. Under this philosophy, we pursue continuous improvement and problem prevention to fulfill our social responsibilities and achieve sustainable development in corporate safety and health. |
Short-term goal | 1. The number of occupational disaster cases in 2024 is zero. 2. Promote the safety and health digital learning platform, providing 2 hours of annual training for all employees. 3. Obtain more safety-related certifications or professional qualifications. |
Medium- and long-term goals | 1. Achieve the goal of zero work injuries and zero accidents. 2. Create a healthy workplace to promote the physical and mental well-being of employees. |
Course of action | 1. Corporate Governance: The Occupational Health and Safety Management System (ISO 45001:2018) is introduced for compliance with occupational safety-related regulations and to ensure system effectiveness. The company continues to improve to build up a work environment that allows employees to work without concern. “Occupational Safety Encouragement Guidelines” are drafted to encourage employees to fulfill work safety. We have established the“Management Regulations for Hazard Identification and Risk Assessment, ” which utilize graded control to plan operational safety control measures, minimizing risks to the lowest level.2-1. Personnel: Honesty and integrity are the core values for work ethic and regulation compliance. They are constructed through the drafting of a series of regulations, realization and implementation, self-review, smooth report channels, and whistle-blower protection. Self-review of the compliance situation is conducted through an annual internal control self-assessment. Guidelines for colleagues to comply with during the execution of business are drafted. All colleagues of respective companies of the Group, regardless of their position, job grade, or location, are requested to comply with the “Integrity Operation Code of Conduct, Moral Behavior Guidelines,” which include contents of work environment guidelines, equal opportunities, confidentiality terms, prohibition of a part-time job, avoidance of conflict of interest, gift offering or receiving, business manners, respect for employees and clients, report, protection, exemption and so on. The purpose of this is to obtain the public’s trust, enhance corporate image, and ensure the company’s sustainable operation and development.2-2. Education and Training: To enhance colleagues’ work ethics and regulation compliance awareness, the company takes references from laws and internal requirements and designates the Department of Health and Safety to collaborate with other responsible departments in conducting routine regulation training on colleagues of different departments/job grades. Corresponding training was given to colleagues with different responsibilities. Training included new employee training, on-the-job training, physical courses, promotion from respective units, and external training. In the meantime, through monthly health and safety promotion in plants and the company’s internal web page, compliance guidance is provided to allow colleagues access to health and safety knowledge from time to time.3. Environmental Health and Safety: The company safeguards corporate internal occupational safety and workplace safety. Through continuous monitoring of environmental management together with an occupational health and safety control system, the company fulfills a corporate obligation and responsibility through an environmental health and safety management system (environmental protection, health and safety, and prevention of occupational hazards). |
Results | Achievement of 2023 Goals: 1. Occupational Accident Incidents: Reduced occupational accidents to four cases, demonstrating our commitment to improving occupational safety and moving steadily towards the goal of “zero incidents, zero occupational accidents. 2. On-the-Job Training: Held 43 on-the-job training sessions with a total of 458 employees participating, accumulating a total of 5,099 training hours, achieving an average of at least 11 training hours per person. 3. Health Promotion: Conducted a health promotion weight loss competition with 22 employees participating. The total reduction in body fat percentage reached 32.5%, and the success rate of weight control among participants was 85.7%.Other Achievements: External Education and Training: 18 employees obtained safety and health-related certifications. Occupational Safety and Health Experience Hall: 25 senior executives visited the Ministry of Labor’s Occupational Safety and Health Experience Hall. Coordination Organization Meetings: Held regular coordination meetings with 30 subcontractors to ensure compliance with safety and health qualifications. Blood Donation Campaign: 65 participants, donated a total of 76 bags of blood. |
Responsible unit | Health & Safety Management Department |
Occupational Health and Safety Management System
Our three plants (Shulin Plant, Yingge Plant, and Dongshan Plant) comply with labor location requirements of national regulations and introduced an occupational health and safety management system (ISO 45001:2018) in 2021 and obtained third-party certification. We constructed a new R&D building in 2023, dedicated to technological research and innovation. To ensure that the occupational safety management level of the new R&D building meets the company’s standards, we have implemented the same occupational safety management system in its operations. This includes hazard identification and risk assessment, as well as the establishment of appropriate control measures to ensure workplace safety within the R&D building.
To ensure the comprehensive implementation of the occupational safety and health management system, we have applied it extensively across our three main plants—Shulin, Yingge, and Dongshan Plant, including the newly constructed R&D building.
Occupational Health and Safety Committee
The company establishes “The Occupational Health and Safety Committee” by the Occupational Health and Safety Management Guidelines. The percentage of commissioners elected by labor representatives is higher than one-third as required by laws.
This committee holds meetings regularly once each quarter. Labor representatives will speak for all employees and discuss related issues of environmental protection, health, and safety with heads of management levels.
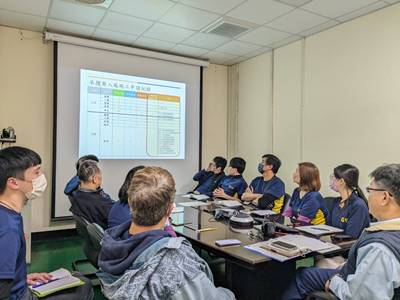
Region | Plant | Total Number of Commissioners in Health and Safety Committee | Number of Labor Representatives | Labor Percentage | Number of Meetings / Year |
---|---|---|---|---|---|
Taiwan | Shulin | 11 | 4 | 37% | 4 |
Yingge | 11 | 4 | 37% | 4 | |
Dongshan | 11 | 7 | 63% | 4 |
Contractor Management
In terms of management of contractor safety, the company establishes a “Contractor Management Process” with contents including education and training before entering the plant, holding communication coordination meetings, and conducting danger notifications. Construction will only be allowed after the construction application form is approved before construction. Supervision of construction safety has been enhanced. (In 2023, we held a coordination meeting with 30 regularly cooperating contractors to improve compliance with the internally established “Contractor Management Procedure” regulations. During the meeting, we required contractors to provide relevant safety and health qualifications and certifications.) These measures aim to ensure that third-party contractors adhere to safety management procedures, thereby ensuring the overall safety of the workplace.
Danger Identification and Risk Assessment
Danger Identification
To ensure workplace safety, we drafted “Management Guidelines for Danger Identification and Risk Assessment” with contents including matters of personnel, location, and facility for various operation activities that may be affected by organization operation as well as operation location not directly controlled by the organization. These matters will all be implemented by the guidelines.
01 / Execution of Danger Identification
Respective units conduct investigations on activities in areas under their management for danger identification and recording on the “Investigation Form.”
02 / Confirmation of Investigation Form
Representatives for occupational health and safety management confirm the completeness, accuracy, and reasonableness of the “Investigation Form.”
03 / Risk Assessment
Respective units fill in assessment forms on dangers identified.
04 / Confirmation of Assessment Form
Representatives for occupational health and safety management confirm the completeness, accuracy, and reasonableness of the “Assessment Form.”
05 / Filing of Assessment Form
Approved “Assessment Form” will be filed by the occupational health and safety unit.
06 / Summary of Risk Danger Levels
Plant management convenes related personnel for discussion, selection, and summarization of the “Control List.”
07 / Risk Control
This will be reported and reviewed in annual management review meetings.
Risk Assessment
Each year, we conduct occupational safety risk assessments, with safety and health management personnel responsible for internal training. The training includes guiding each unit in evaluating related raw materials, products, activities, and services, and identifying potential hazards that could cause personnel injury or equipment loss. After assessing the risk level, we implement graded management controls based on the risk classification, set improvement goals, and monitor the effectiveness of control measures to reduce the likelihood of hazards occurring.
Hazard identification and risk assessment data were provided, with a total of 671 hazard identifications conducted across all plants: 231 at the Yingge plant, 217 at the Shulin plant, and 223 at the Dongshan plant. Based on the hazard identification results, we identified higher-risk items and developed management plans for improvement. A total of 30 improvement plans were formulated, including safety improvements for on-site working environments, all of which have been completed.
Respective plants continue to conduct cause analysis and strengthen education training on every occurrence of incidents. They also keep track of improvement schedules on respective occupational injury incidents. When necessary, occupational doctors or nurses will offer related information on health counseling and medical assistance to colleagues.
Occupational Disaster Incident
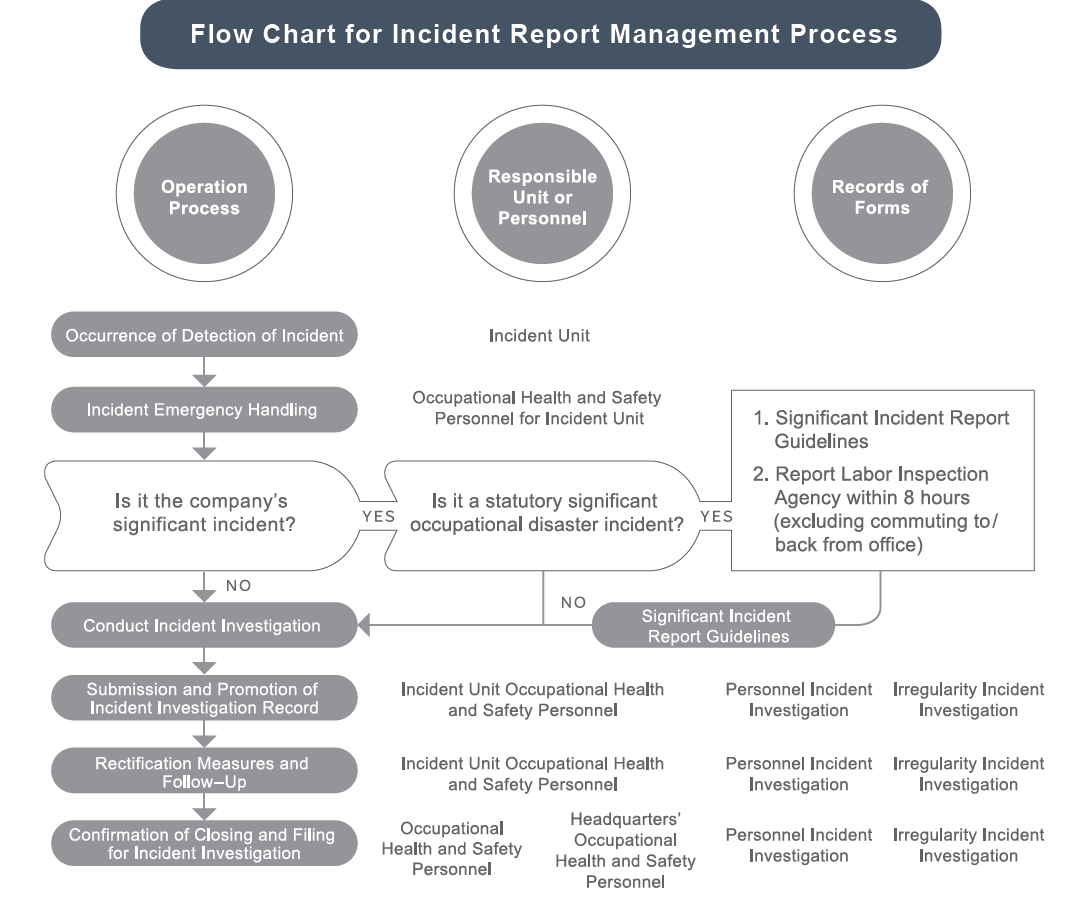
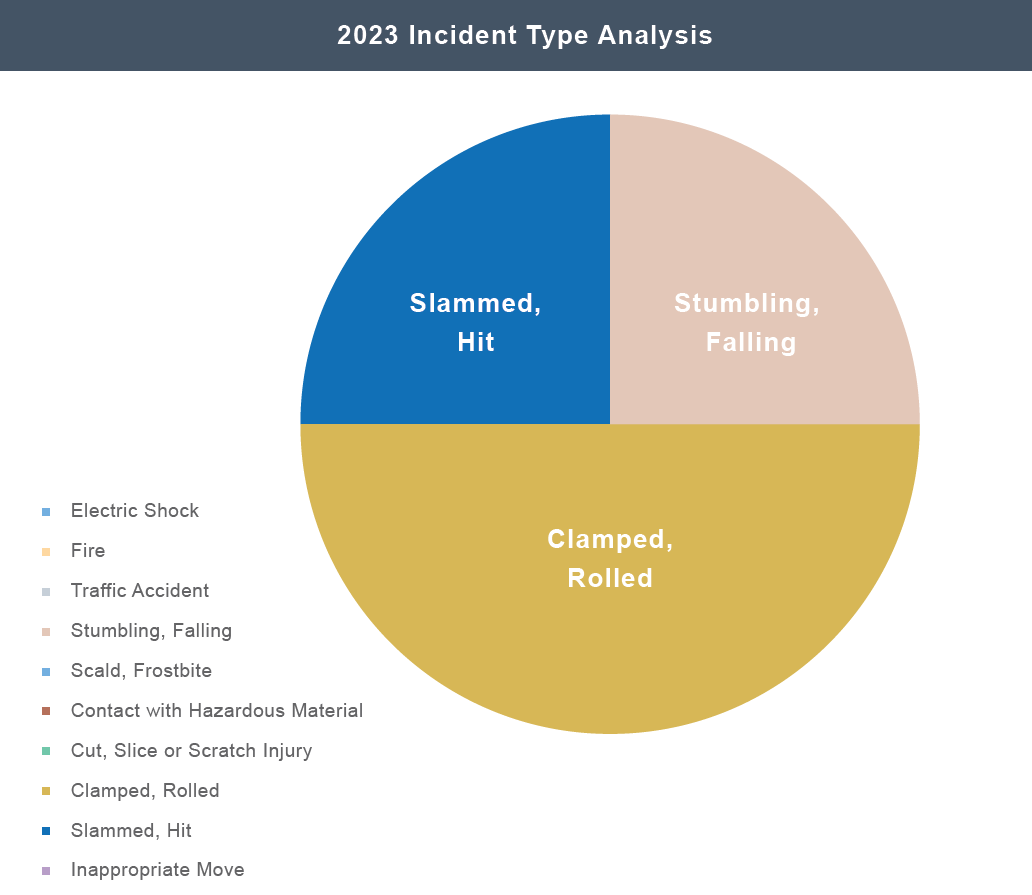
The company immediately has conducted emergency incident handling and notification to mitigate damage to the lowest level. The company also investigates and reviews causes of occurrence as well as prevention measures to prevent similar incidents from occurring again.
Through further analysis of 2023, it was observed that the majority of occupational injury types were from employees’ insufficient danger awareness, with occurrences of clamped and rolled accounting for the most part.
To reduce the occurrence of incidents, health and safety operation standards were established in 2020 to enforce comprehensive strengthening safety mechanisms for machines and equipment.
The effectiveness of these measures was evident, as seen in the comparison of the annual number of incidents and lost workdays: number of incidents across plants has dropped from 19 in 2020 to 4 in 2023, and number of days for work loss has dropped from 408 days in 2020 to 142 days in 2023.
We will continue our efforts to ensure workplace safety through continuous monitoring, process improvements, and enhanced training, aiming to reduce the occurrence of accidents.
Occupational Health and Safety Management Measures
Occupational Health Service
The company provides health examination benefits better than the ones required by laws.
On-site health counseling assistance is provided. Each month, occupational doctors are arranged to visit plants to conduct counseling and offer the following services:
- Conducting respective units’ related danger assessment and suggestions based on requirements from the occupational health and safety unit:
- Providing injury/disease counseling, assessment, and related suggestions to employees;
(For instance, counseling, assessment, and judgment of health examination hierarchical management for general health examination/special operation examination, review and assessment of human factor danger, physical examination/health examination irregularity assessment, and so on.) - In terms of the engineering improvement scheme proposed by occupation doctors, related units will conduct subsequent assessments and improvements accordingly.
- For employees with abnormal findings in a health examination, occupational doctors or occupation nurses shall continue to track their improvement status or assist in recommending their work adaptive adjustment.
Item | Party | Time Required by Laws | Expense Assumption | Company Benefits |
General Physical Examination (Including Group Meal) |
New Employees | Before New Employee’s Report to Office | Labor/Management Negotiation | Expenses assumed by the company. |
Special Health Examination (Noise) |
Special Health-Endangering Operation Personnel | Before New Employee’s Report to Office Duty Change |
Labor/Management Negotiation | Expenses assumed by the company. |
General Health Examination (Including Group Meal) |
Age < 40 | Every 5 Years | Assumed by Employer | All employees may participate in general health examinations each year with expenses assumed by the company. Supervisors may participate in management health examinations each year with expenses assumed by the company. |
Age = 40 ~ 64 | Every 3 Years | |||
Age > 65 | Every Year | |||
Special Health Examination (Noise) |
Special Health-Endangering Operation Personnel | Every Year | Assumed by Employer | Expenses assumed by the company. |
Occupational Health and Safety Education and Training
To ensure that every worker is familiarized with occupational health and safety-related regulations and the company’s health and safety management mechanisms, KYF regularly provides occupational health and safety-related education and training to introduce health and safety culture and concepts.
We organized a total of 25 on-the-job training courses, with 1,946 attendees and a total of 2,992 training hours in 2022.
We organized a total of 43 on-the-job training courses, with 2,370 attendees and a total of 5,099 training hours in 2023.
This year, we implemented a registration system, allowing employees to choose training sessions based on their interests, needs, and schedules, providing greater flexibility and personalization. This flexible arrangement has contributed to higher employee participation rates and improved training effectiveness.
Notably, the on-the-job training hours have met the regulatory requirement of three hours over three years, demonstrating the company’s commitment to safety and health education and regulatory compliance.
Emergency Incident Handling
The company drafted a “Management Process for Emergency Incident Preparation and Response” and conducted contingency handling by handling processes for presumed scenarios (handling criminal threats and extortion, water and power outages, pandemics, chemical leakage, and so on). The company also complies with guidelines from the Occupational Safety and Health Administration and conducts emergency response drills regularly. The main purpose is to enhance personnel’s capability of responding to emergencies, establish an accurate handling process, and provide timely action guidelines when disaster strikes to ensure personnel and environment’s safety, maintain plant normal operation, and mitigate possible disaster losses from accidents to the lowest level.
Employee Health Management
Health Examination
- Each year, the company commissions large hospitals to conduct health examinations to protect employee’s health and report to competent authorities for reference. The health examination rate for 2023 reached 100%, a total of 395 employees were required to health examinations, and all 395 completed the check-ups, covering colleagues in the R&D Building, Shulin, Yingge, and Dongshan Plant.
- In addition to general health examination items, special health examination is also conducted by labor health protection requirements from the Ministry of Labor.
Hierarchical management is adopted in health management. Most cases are classified as tier 1 or tier 2 management and few cases are classified as tier 4 management after doctor’s examination. Based on this hierarchical management (tier 1 to tier 4), plant nurses will provide care or suggestions depending on the employee’s health examination results. In the event of cases with irregularity detected from special health examination, referral to hospital for further examination, routine tracking, or medical treatment will be arranged accordingly.
Implementation of Occupational Disease Prevention
KYF continues to build up a work environment of health and safety, reviews work items repeatedly, and collaborates with external experts based on risk identification measures hoping to locate 5 major hazardous factors chemical factor, physical factor, human factor, biological factor, and social/mental factors that may lead to occupational disease, and to implement corresponding prevention measures accordingly.
Human Factor
Explanation: Collaboration with occupational doctors in conducting on-site visits.
- To enhance workplace ergonomics, thereby improving work efficiency and reducing the burden on workers.
- The company collaborates with occupational doctors in conducting on-site visits.
- Occupation doctors are arranged to visit operation sites in plants and offer related suggestions for implementation of improvement accordingly. This occurs once a month
Mental Factor
Explanation: On-Job Health Examination: Mental Health Inventory, Copenhagen Burnout Inventory
- Management scheme for continued improvement in cardiovascular disease prevention
- A health management system is utilized to combine employee health examination results and working hour status for assessment of health risks.
- On-Job Health Examination: mental health inventory (10-year risk assessment), Copenhagen Burnout Inventory /once every year
Biological Factor
Explanation: Real-Time Tracking Announcement Information from the Center for Disease Control and Health Promotion Administration. Timely Provision of Health Education Latest Information in Response to News.
- Strengthened workplace cleanliness and hygiene standards to reduce the spread of biological hazards.
- Regular cleaning and disinfection are conducted, especially in areas prone to microbial growth such as restaurants, bathrooms, etc.
- Provided employees with appropriate personal protective equipment (PPE) such as masks, gloves, etc., to minimize direct contact with biological hazards.
- Real-time tracking of announcements from the Center for Disease Control and Health Promotion Administration; Timely Provision of Latest Health Education Information in Response to News.
- The company continues to pay attention to real-time information on respective countries’ pandemic situation, establishes preparation and response guidelines for communicable diseases, and drafts KYF Company’s pandemic prevention strategies.
(For instance: For COVID-19, the company provides pandemic prevention materials of multiple fixed and hand-held temperature thermometers, hand sanitizer, protective clothes, masks, face masks, quick tests, and conducts whole-plant environment sanitization. The company also establishes respective departments’ self-health management monitoring forms and keeps these records for reference purposes.)
Physical Factor
Explanation: We establish a good working environment and conduct regular workplace environment monitoring, as well as periodic on-the-job training.
- Continuously implement risk assessments of hazard factors and improve workers’ working conditions by adjusting the working environment.
- Environmental air conditioning is increased to enhance comfort in an indoor environment.
- The company establishes a good operation environment and regularly conducts operation environment monitoring as well as random on-job training.
Chemical Factor
Provide general hazard education and training on chemicals to ensure that employees understand the hazards of chemical use and preventive measures.
- Establish a chemical inventory, hazard labeling, and safety data sheet disclosure, and implement management for the use of chemicals. Ensure the implementation of a chemical use management mechanism.
- Regularly conduct chemical assessments and classification management, and based on the classification results, adopt appropriate management methods and exposure control measures.
- Provide general hazard education and training on chemicals to ensure that employees understand the hazards of chemical use and preventive measures.
Worker Health Promotion
- Comprehensive Health ManagementKYF’s comprehensive health management encompasses the implementation of occupational disease prevention and the promotion of employee’s health. Through the work environment, health risks are controlled, employee’s physical and mental health is maintained and their balance between work and life is enhanced accordingly.According to the 2021-2022 plant-wide health checkup report, the proportion of people with abnormal body mass index (BMI), waist circumference, and total cholesterol is relatively high.The literature points out that abnormalities in the above health indicators are likely to lead to an increased risk of chronic diseases. Therefore, these health problems urgently need to be effectively controlled.With the internal resolution and support of superiors, a health promotion activity will be held in 2023: “Healthy Workplace ~ Weight Loss Competition”, aiming to inspire all colleagues to fight obesity together and create a happy and healthy workplace environment.
Patrol Operation Management
The company drafted “Patrol Operation Management Guidelines” and the Health and Safety Management Department will conduct critical area patrol as well as random checks on respective departments. Critical area patrol includes weekly random patrol on machine rooms on respective floors, contractor on-site construction’s compliance with the application form, and random checks on machine safety equipment. The on-site department conducts patrol based on the contractor’s operation patrol form which includes general requirements, falling, electric shock, falling objects, and fire prevention to enhance various operation safety while ensuring personnel’s life safety and health. For deficiency matters, the “Health and Safety Violation Handling Form” will be issued accordingly. For departments with fail to rectify after notice has been issued 3 times or for departments with immediate risk of danger occurrence, they will be requested to suspend operation and improve accordingly within the deadline.
- Evaluate the implementation of inspections on each floor and discuss possible risks at weekly supervisor meetings.
- In 2023, during inspection operations, it was observed that the areas where employees commute to and from work overlap with the raw material transportation zones, creating safety risks such as collisions with vehicles.
- To improve safety, pedestrian walkways, corner mirrors, and warning signs have been added within the walking area, and it is emphasized that the speed limit for vehicles passing through this area shall not exceed 6 kilometers.
- These measures are designed to provide employees with safer walking routes to reduce the likelihood of accidents.
Manufacturing Process Safety Management
Manufacturing Process Safety Management has 7 major items including rectification and prevention, education and training, management on contracting, management of operation change, occupational disaster incident investigation, emergency plan, and contingency and compliance audit for maintaining equipment completeness and personnel’s familiarization on equipment (including protection gear). Through the implementation of risk assessment, labor participation, hot work permit, change management, incident investigation, and compliance audit, the company understands plant equipment and personnel operation’ best status and therefore this reduces occurrence possibilities and severity of various risks. Encourage employees to report near-miss incidents as a basis for reviewing potential hazards and eliminating risks to prevent accidents and injuries.
- Through the collection of safety management data, risk assessment of process machinery and equipment, and personnel operations
- In 2023, the relevant regulations on overhead crane operation, ladder combination, and wearing of safety helmets were re-examined, and employees were educated on potential hazards.
- This initiative aims to enhance the safety of all operations, ensuring that risks are minimized during the operation of machinery and equipment as well as during personnel activities.
- Through redesigned rules and employee education, the company works to keep the work environment safe and minimize potential injuries.
Other Related Operation Guidelines
To prevent and mitigate occupational health and safety impacts directly related to business relationships, related operation guidelines are drafted accordingly such as personal protective equipment management guidelines, management guidelines for operation environment monitoring, special operation management guidelines, and management guidelines for labor health protection. The safety of the operation environment is maintained through systematic management. Additionally, to actively promote workplace safety, we have established a safety award and penalty management system. We track workplace accident cases across various units and provide collective rewards to units with outstanding performance, creating a culture of occupational safety and health through group incentives.
- By the Occupational Health Protection Regulations, we conduct general and special health examinations annually, surpassing the frequency required by current regulations, to gain a deeper understanding of employees’ physical conditions.
- In 2023, the most notable abnormal index in the health examination was Body Mass Index (BMI). As a result, we have planned a weight loss program with monetary rewards to encourage employee participation.
- The goal of this health promotion activity is to encourage employees to establish good exercise habits, improve their health, and, consequently, enhance the overall physical health level of all employees.