KYF
Environment
Energy Management
能源管理作為金元福落實環境政策的核心議題,也是達成脫碳路徑的雙支柱之一。
Energy management symbolizes a core task of our environmental policy and one of the two pillars of our decarbonization pathway strategy.
Energy Management
Energy management symbolizes a core task of our environmental policy and one of the two pillars of our decarbonization pathway strategy.
We have made substantial investments in energy conservation equipment and researched renewable energy acquisition to honor our commitment to RE 100, reduce our carbon emissions, and maximize ou r positive influence on the environment.
Impact – Economy
Carbon taxes / fees result in rising potential product prices

Impact – Environment
Commitment to emission reduction is conducive to mitigating the greenhouse ef fect.
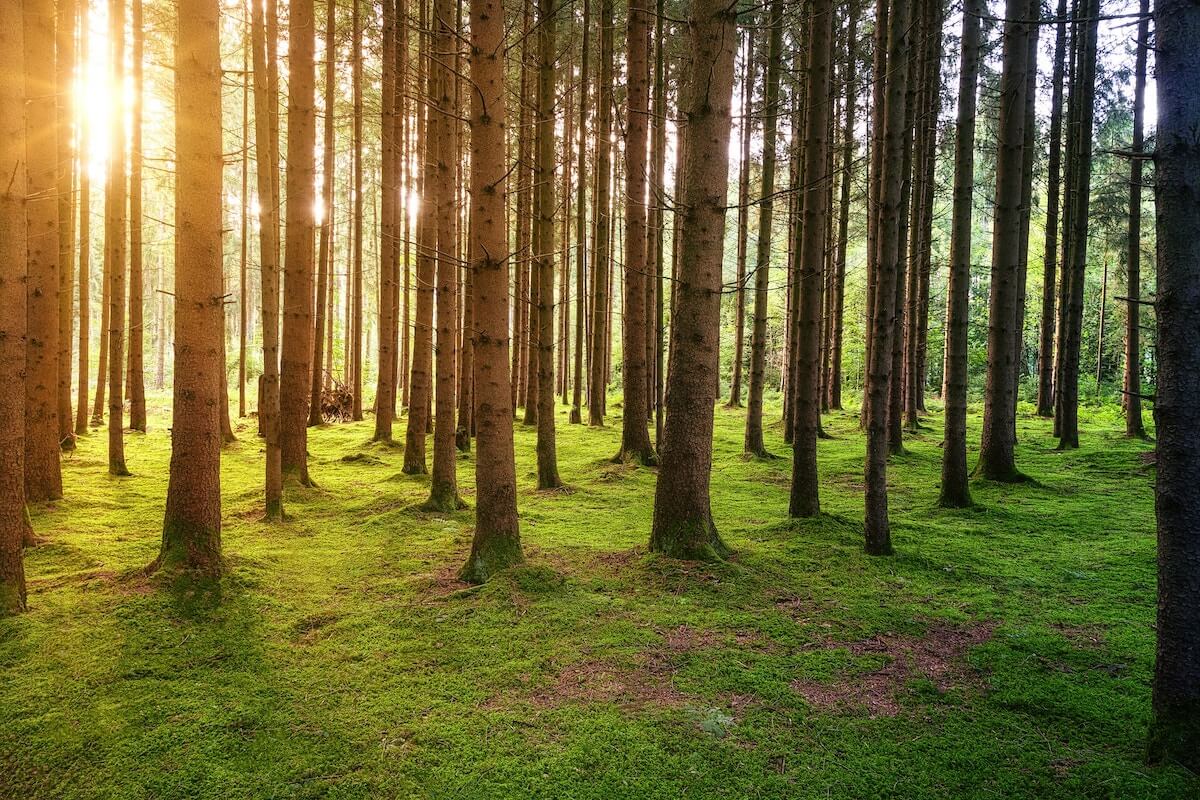
Policy and Commitment
Set up a carbon neutrality path to track continuing efforts in decreasing power consumption and increasing renewable energy share per unit.
Short – term goal
Decreasing year –over–year (YoY) power per –unit consumption by 1.0% in 2024.
Medium – and long–term goals
Achieving RE100 commitment, 60% renewable energy in 2030, 90% r enewable energy in 2040, 100% renewable energy in 2050.
Course of action
We maintain the effectiveness of the ISO 50001 Energy Management System at the Dongshan plant and continue to promote internal
ESG improvement proposals.
Results
- We has maintained the ef fectiveness of the ISO 50001 Energy Management System at the Do ngshan plant in 2023.
- Total energy savings of 4,423,304 kWh achieved through internal energy conservation initiatives in 2023.
- Decreasing year–over–year power per –unit consumption by 4.69% in 2023.
Responsible unit
Sustainable Development Department
Energy Consumption
Due to our process requirements, our main energy source is purchased electricity. Power conservation therefore represents our core strategy to maximize our positive influence in the environmental dimension. The scope of our energy consumption reporting in 2023 encompassed the Shulin, Yingge, and Dongshan plants, as well as the R&D building, achieving a coverage rate of 100%.
Energy consumption conditions in 2023
Energy categories | Type | Shulin Plant | Yingge Plant |
Dongshan Plant |
R&D Building | Total | MJ Coefficient | Total energy consumption (MJ) |
---|---|---|---|---|---|---|---|---|
Total energy consumption (MJ) |
Non–renewable | 6,596,126.00 | 34,591,152.00 | 49,291,921.00 | 1,775,600.00 | 92,254,799.00 | 1kWh=3.6*(10^–6)TJ | 332.1172764 |
Diesel (liter) | Non–renewable | 19,728.85 | 1,945.18 | 4.00 | 0.00 | 21,678.02 | 1kcal= 4.187*(10^–9)TJ | 0.0000908 |
LPG (liter) | Non–renewable | 0.00 | 43.632 | 345.42 | 0.00 | 389.05 | 1kcal= 4.187*(10^–9)TJ | 0.0000016 |
Gasoline (liter) | Non–renewable | 1,087.03 | 4,503.46 | 0.00 | 0.00 | 5,590.49 | 1kcal= 4.187*(10^–9)TJ | 0.0000234 |
Solar power (kWh) | Renewable | 0.00 | 11,645.00 | 0.00 | 17,821.00 | 29,466.00 | 1kWh=3.6*(10^–6)TJ | 0.1060776 |
Total | 332.2234698 |
Note:
- The coefficients and indicators listed above have been derived from “Wi dely Used Calorific V alues in International Energy Statistics” in the 2018EnergyStaH andBook of the Bureau of Energy (1 liter of Diesel = 8,400 kcal, 1 liter of LPG = 6,635 kcal, 1 liter of gasoline = 7,800 kcal)
- Gcal, a unit of energy that frequently appears in international energy statistics, can be converted into the TJ coefficient as follows: 4.187×10–3; Kcal =1,000cal, Gcal = 1,000,000,000
- All three sites are equipped with self – used solar energy facilities. The green energy certificates obtained in 2023 were as follows: (certificate verification: https://www .trec.org.tw/certification)
– Yingge Plant Solar Power Generation Certificate number: 21SP0031 – B023000001~11
– R&D building Solar Power Generation Certificate number: Currently in the application process, expected to be completed by September 2024.
The electricity generated by the solar facilities within the th ree plants were as follows:
Solar Power Generation List | |||||||
Electricity Unit (kWh) | |||||||
Category | Plant /Building | Taipower Customer Number | Installed Capacity (kW) | 2020 | 2021 | 2022 | 2023 |
---|---|---|---|---|---|---|---|
Feed–In Tariff | Dongshan | 03–44–6362–99–4 | 498.928 | 442,880 | 448,512 | 407,440 | 472,672 |
Feed–In Tariff | Dongshan | 03–44–6362–98–3 | 288.05 | 257,628 | 288,720 | 263,172 | 285,900 |
Feed–In Tariff | Dongshan | 03–44–6361–99–3 | 187.68 | ––– | 97,408 | 171,968 | 181,940 |
Feed–In Tariff | Yingge | 05–81–5596–98–1 | 458.01 | 400,544 | 510,944 | 460,288 | 458,552 |
Self–Consumption | Yingge | 05–81–5596–11–7 | 10.065 | ––– | ––– | 10,995.7 | 11,645 |
Self–Consumption | R&D | 05–81–5599–11–0 | 104.14 | ––– | ––– | ––– | 17,821 |
Total power consumption broken down by plants in the period from 2021–2023:
Plant | 2021 | 2022 | 2023 | Difference between 2023 and 2022(percentage)2021 |
---|---|---|---|---|
Shulin Plant | 12,444,940.6 | 10,050,658 | 6,596,126 | – 52.37% |
Yingge Plant | 40,866,144 | 36,675,488 | 34,591,152 | – 6.03% |
Dongshan Plant | 56,019,287.4 | 49,855,056 | 49,291,921 | – 1.14% |
R&D Building | ––– | ––– | 1,775,600 | ––– |
Comparison of two years’ dif ferences | 96,581,202 | 92,254,799 | – 4.69% |
It has been determined upon analysis that despite the aforementioned year–over–year drop of 4.69% caused by a decline in our output, the reduction is attributed to the effectiveness of improvement proposals, resulting in a decrease of about 5% in electricity consumption per ton of production. We will continue to pursue internal energy –saving improvements in the future.
Average power consumption per ton output in 2021–2023:
2021 | 2022 | 2023 | |
---|---|---|---|
Average power consumption per ton output of finished goods (kWh) |
1,656.0 | 1,684.0 | 1,592.9 |
Note:
It had been detected by the ESG Committee that shipment volume was not an accurate measure of production– related power consumption; it was therefore decided to replace shipment volume with finished good output volume for power consumption calculations in 2022.
2021: [Power consumption of all plants – (Office power consumption + Dormitory power consumption)]/
[Total shipment volume of finished goods in all material categories*Sum of all material density parameters converted into PET density]
2022: [Power consumption of all plants – (Office power consumption + dormitory power consumption)]/
[Total output volume of finished goods in all material categories*Sum of all material density parameters
converted into PET density]
Correction:
Power consumption calculated based on shipment volume in 2021 has been determined to be an inaccurate representation of production–related power consumption. Shipment volume was therefore replaced with output volume for calculations in 2022.
Average energy consumption per ton output of finished goods in th e period from 2021 to 2023:
Year | 2021 | 2022 | 2023 |
---|---|---|---|
Annual total (MJ) | 393,601,710.64 | 347,881,990.45 | 332,223,469.8 |
Total weight in tons based on converted density for each material | 71,989.15 | 57,463.56 | 56,800.49 |
Average energy consumption per ton output of finished goods (MJ) (Energy Intensity) | 5,467.51 | 6,053.96 | 5,848.95 |
Note: 1kWh = 3.6 MJ; 1kcal=4.187*(10^-3) MJ
Correction: The 2022 sustainability report contains incorrect data for 2021 and 2022, and has been revised accordingly .
The YoY drop in energy intensity values in 2023 can be attributed to t he replacement of Diesel –powered forklifts and the ef fects of improvement initiatives.
Average energy consumption per ton output of finished goods (MJ) (Energy Intensity)
Power Conservation and Energy Management
All our manufacturing sites report their energy consumption data to the Bureau of Energy of the Ministry of Economic Affairs on an annual basis under the provisions outlined in Article 12 of the Energy Administration Act. Looking back on the past three years, the average annual power– saving rate of all plants overachieved the legal requirement of 1%.
Year | Shulin Plant | Yingge Plant | Dongshan Plant | R&D Building |
---|---|---|---|---|
2020 | Power saving rate for the respective year: 2.4% Average annual power saving rate: 1.9% |
Power saving rate for the respective year: 1.8% Average annual power saving rate: 1.5% |
Power saving rate in the respective year: 1.3% Average annual power saving rate: 1.7% |
— |
2021 | Power saving rate in the respective year: 0.0% Average annual power saving rate: 2.2% |
Power saving rate in the respective year: 1.5% Average annual power saving rate: 1.5% |
Power saving rate in the respective year: 1.3% Average annual power saving rate: 2.1% |
— |
2022 | Power saving rate in the respective year: 0.11% Average annual power saving rate: 1.95% |
Power saving rate in the respective year: 0.45% Average annual power saving rate: 1.45% |
Power saving rate in the respective year: 1.7% Average annual power saving rate: 1.88% |
— |
2023 | Power saving rate in the respective year: 0.93% Average annual power saving rate: 1.9% |
Power saving rate in the respective year: 0.32% Average annual power saving rate: 1.34% |
Power saving rate for the respective year: 0.8% Average annual power saving rate: 1.73% |
Complete preliminary declaration |
Note: Under the amendment to the Regulations Governing the Formulation of Energy Conservation Targets and Implementation Plans by Energy Users adopted by the Ministry of Economic Affairs on December 25, 2019, energy users with a contract capacity of over 800kW are required to achieve an average annual power saving ra te of at least 1.0% in the ten years from 2015 –2024. The power saving rate based on energy conservation targets and implementation plans in the respective year must exceed 1% (total power savings equal the sum of all power savings resulting from power conservation measures implemented by the Company). Completion and reporting of energy–saving
Completion and reporting of energy–saving improvement projects for the year 2023, including cases of electricity savings and energy efficiency measures:
Plant | Item | Initiative | Energy Savings (kWh) | Total Energy Consumption (MJ) |
---|---|---|---|---|
Dongshan Plant | 1 | Pressure stabilization and flow improvements implemented for compressed dry air (CDA) utilized for processes | 59,850.000 | 0.2155 |
2 | Energy-saving plan for lighting fixtures on the first floor of Building A at the Dongshan plant | 20,704.000 | 0.0745 | |
3 | Shared Pipeline to Reduce the Use of One Mold Temperature Control Unit | 3,724.000 | 0.0134 | |
4 | Shared Pipeline for Vacuum Machine (DA09~DA12) | 23,712.000 | 0.0854 | |
5 | Shared Pipeline for Vacuum Machine (DA05~DA08) | 16,473.667 | 0.0593 | |
6 | Dongshan Plant Compressed Air Energy Saving Plan 2 (Power System Allocation during Plant Shutdown) | 114,077.833 | 0.4107 | |
7 | Dongshan Plant Air Compressor Pressure Storage Tank with No-Discharge Drainage System | 23,343.750 | 0.084 | |
8 | Electric Furnace Energy-Saving Plan | 133,342.000 | 0.48 | |
Yingge Plant | 1 | Energy-saving motor upgrade for the crusher: IE1 to IE3. | 13,356.000 | 0.0481 |
2 | Addition of a rear feed port to the crusher. | 4,400.000 | 0.0158 | |
3 | Improvement in stabilizing compressed air for processes. | 93,333.333 | 0.336 | |
Shulin Plant | 1 | Demolition of exhaust hood and cessation of exhaust fan motor. | 51,563.333 | 0.1856 |
Total | 2.0083 |
Note: Coefficients and indicators have been derived from “Widely Used Calorific Values in International Energy Statistics” in the 2018EnergyStaHandBook of the Bureau of Energy: 1kWh = 3.6*(10^-6)TJ.
2020 has been set as the base year for reporting power savings.
To facilitate the systematic implementation of energy conservation, the Dongshan Plant adopted the ISO 50001 Energy Management System in 2022. The plant has determined the order of priority for energy consumption improvement measures based on an energy baseline inventory. Our other plants are projected to follow the example of the Dongshan Plant by adopting ISO 50001 shortly .
In addition to energy–saving reports, internal energy–saving improvement projects are tracked for effectiveness in each quarterly ESG committee meeting. The total number of internal proposals and their performance in 2023 were as follows:
除了節能申報外內部的節能改善案件,於每季 ESG 委員會中對於能源相關的改善做成效追蹤,2022年內部提案成果如下 :
Plant | Number of energy conservation initiatives | Conserved energy in kWh | Total energy savings in kWh | Total energy savings in MJ |
---|---|---|---|---|
Yingge Plant | 9 | 2,998,498.0 | 4,423,304.2 | 15.92 |
Shulin Plant | 4 | 148,481.0 | ||
Dongshan Plant | 14 | 1,276,325.2 |
RE100 Membership
In August 2021, we became an official member of the Climate Group’s RE100 Initiative (media coverage link) and the first (and so far only) plastic container manufacturer to pass the RE100 review process. We commit to achieve 100% renewable electricity by 2050. We have set clearly defined goals of 60% and 90% renewable energy in 2030 and 2040, respectively , to ensure ongoing progress toward the net –zero vision and make a contribution to keeping the global tempe rature rise within 1.5°C.
In 2022, the Dongshan Plant participated in the Demonstration Guidance Project for Energy Management in the Manufacturing Sector organized by the Industrial Development Bureau (IDB) of the Ministry of Economic Affairs. The guidance consultant assisted the plant in gaining a deeper insight into energy management processes and fundamentals with the ultimate goal of giving employees a better understanding of energy management practices and accelerating the implementation process. The plant passed the certification audit for the ISO 500001 Ene rgy Management System in 2022 and continued to maintain its ef fectiveness in 2023.
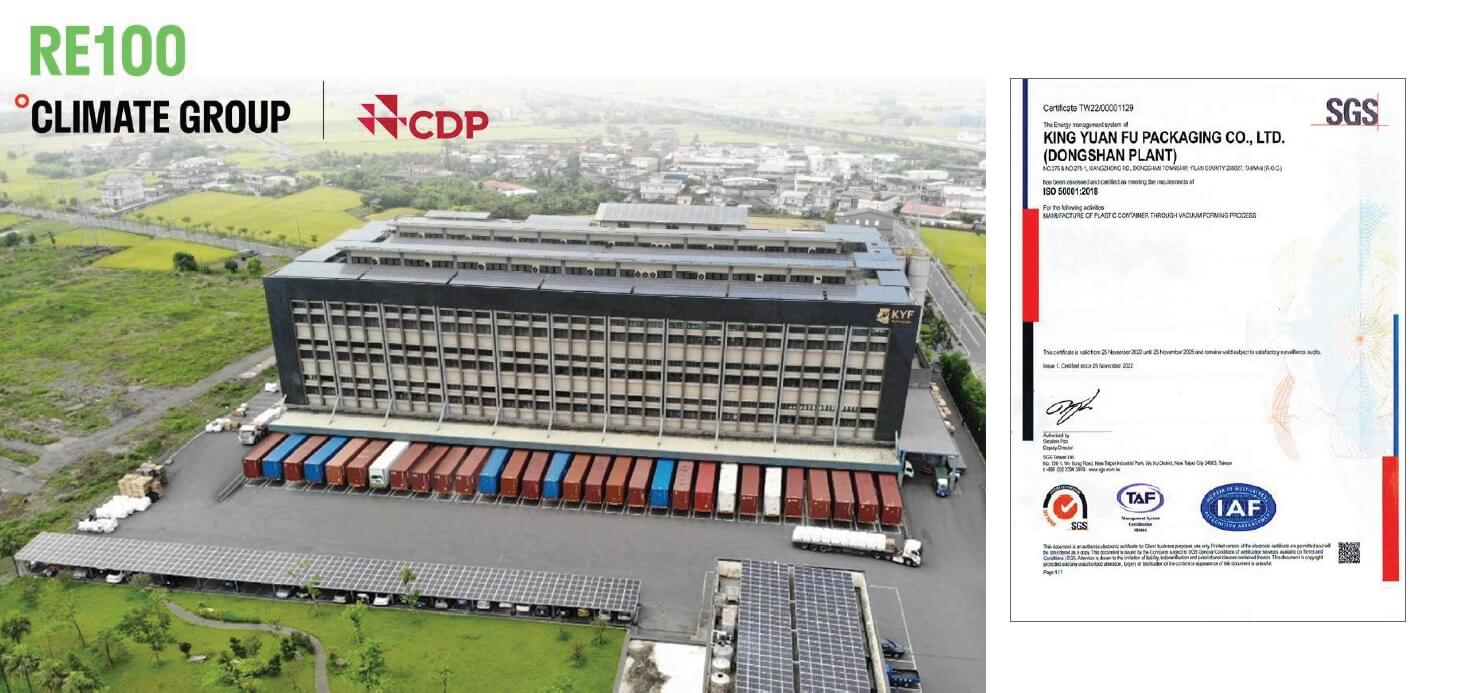